Warning: Undefined array key "coverAlt" in D:\inetpub\webs\veroprojectit\res\x5engine.php on line 1416
Warning: Undefined array key "coverTitle" in D:\inetpub\webs\veroprojectit\res\x5engine.php on line 1417
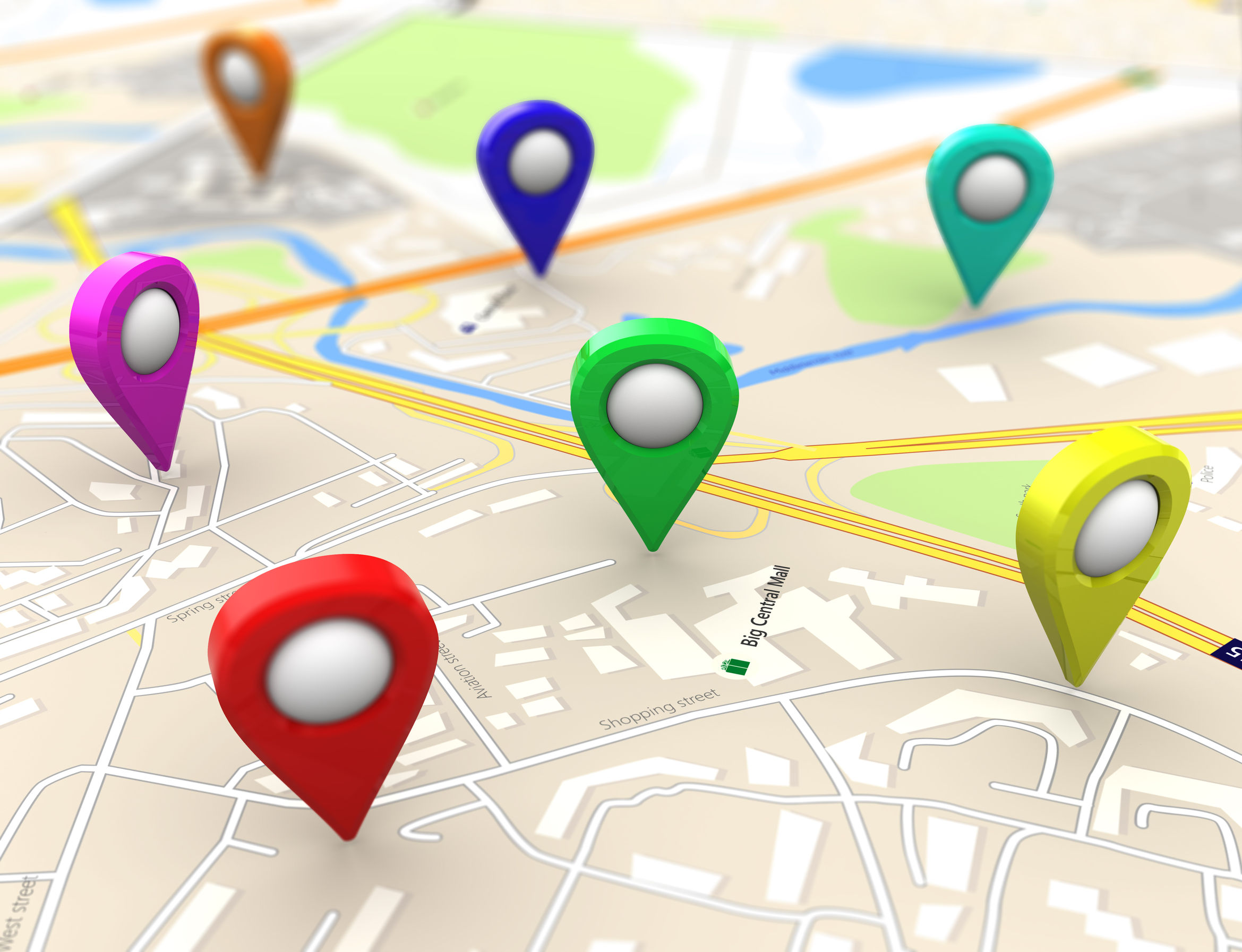
Vero Project apre la nuova sede a Parma e migliora la sua presenza sul territorio.
Warning: Undefined array key "coverAlt" in D:\inetpub\webs\veroprojectit\res\x5engine.php on line 1416
Warning: Undefined array key "coverTitle" in D:\inetpub\webs\veroprojectit\res\x5engine.php on line 1417
Warning: Undefined array key "isHighlighted" in D:\inetpub\webs\veroprojectit\res\x5engine.php on line 1409
Warning: Undefined array key "coverAlt" in D:\inetpub\webs\veroprojectit\res\x5engine.php on line 1416
Warning: Undefined array key "coverTitle" in D:\inetpub\webs\veroprojectit\res\x5engine.php on line 1417
Warning: Undefined array key "isHighlighted" in D:\inetpub\webs\veroprojectit\res\x5engine.php on line 1409
Warning: Undefined array key "coverAlt" in D:\inetpub\webs\veroprojectit\res\x5engine.php on line 1416
Warning: Undefined array key "coverTitle" in D:\inetpub\webs\veroprojectit\res\x5engine.php on line 1417
Warning: Undefined array key "isHighlighted" in D:\inetpub\webs\veroprojectit\res\x5engine.php on line 1409
Warning: Undefined array key "coverAlt" in D:\inetpub\webs\veroprojectit\res\x5engine.php on line 1416
Warning: Undefined array key "coverTitle" in D:\inetpub\webs\veroprojectit\res\x5engine.php on line 1417
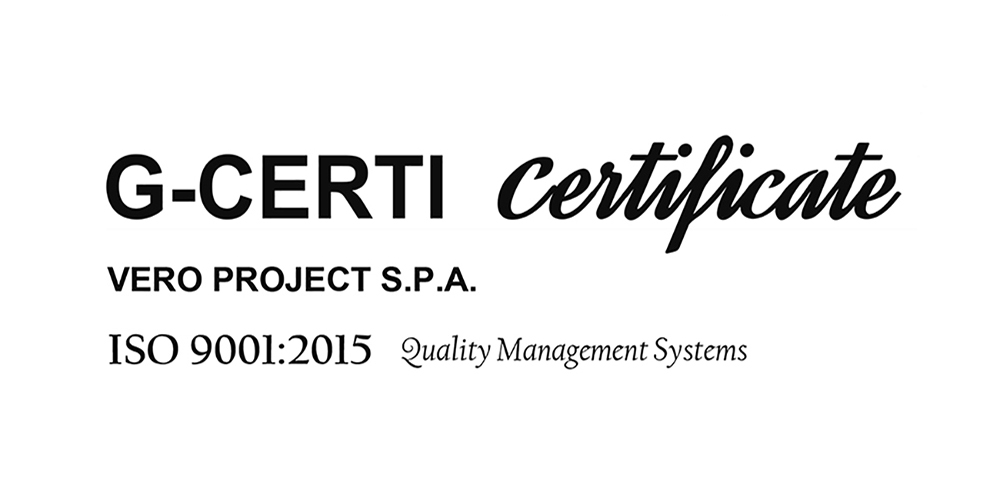
Vero Project ha raggiunto l’importante traguardo della certificazione di qualità ISO 9001 EA 37 ed EA 33
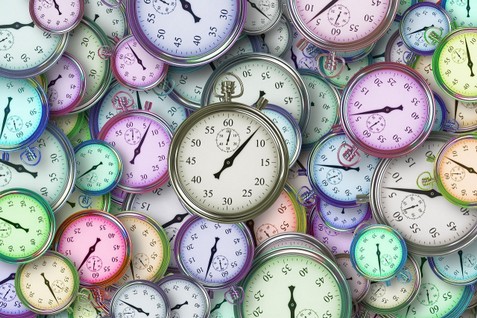
Formare le persone al time management migliora le performance dell'azienda e rende i collaboratori più consapevoli della gestione il loro tempo.
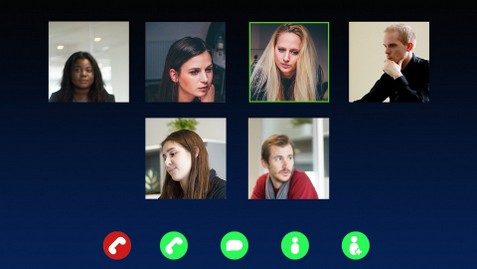
Il COVID 19 ci ha spinto ad utilizzare tecnologie già esistenti ma che per pigrizia e avversione alle novità non eravamo soliti usare.
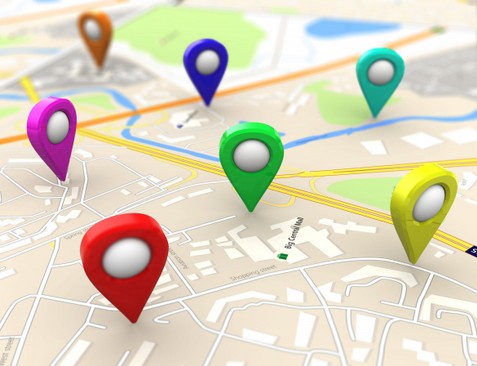
Vero Project Spa per seguire meglio i clienti del Centro Sud, apre la filiale ad Ancona. Il Dr. Stefano Maracci è il nuovo direttore e responsabile di filiale.